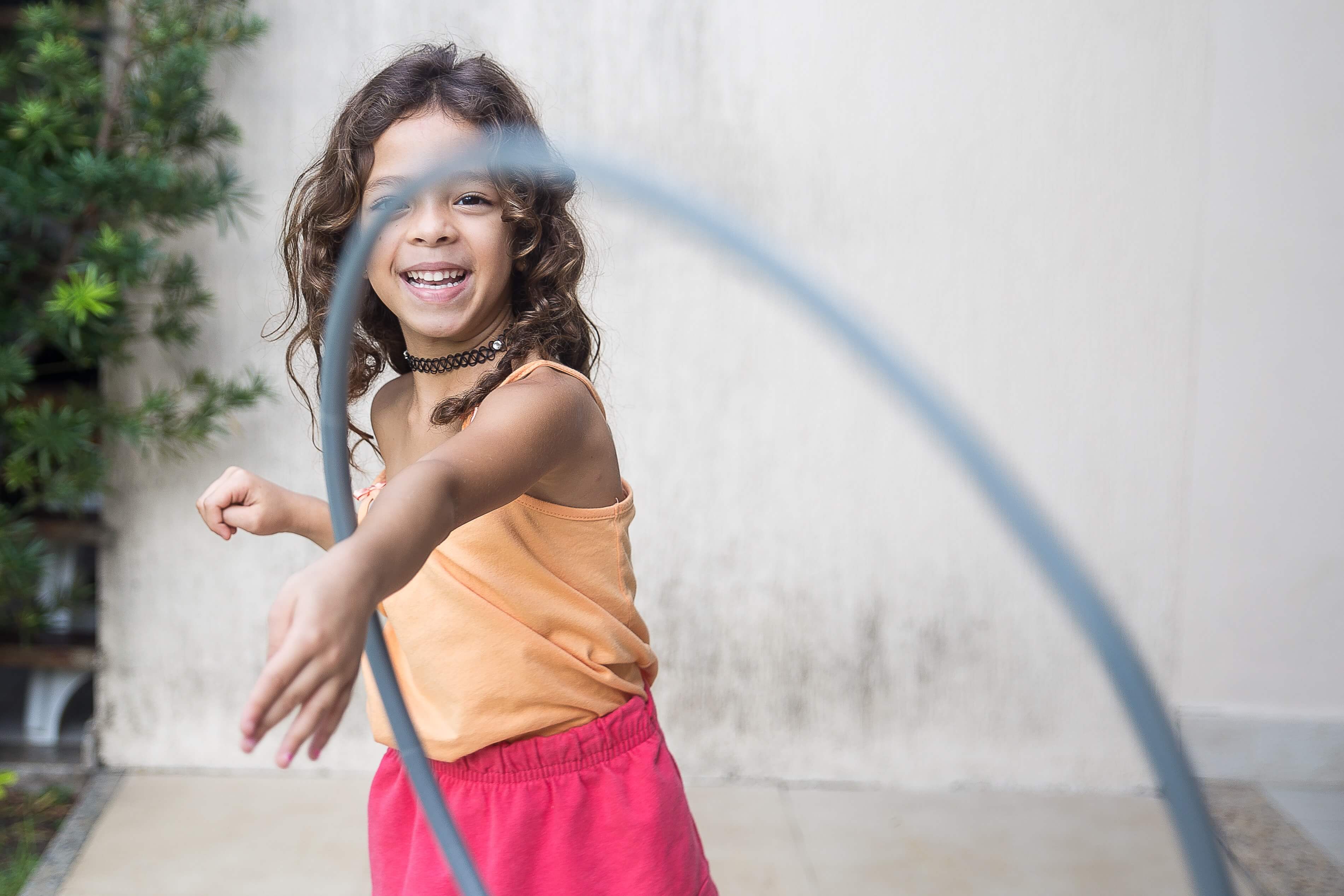
A Culture of Kaizen
Building continuous improvement habits
First there was Scrum, then there was Agile. When Scrum became popular in the mainstream it revolutionized the way work was done. Micro-management moved towards self-managing teams, delegating work to the team moved towards the teams pulling the work. Bliss.
Strangely, it all felt very familiar. That is probably because it was.
Taking a closer look at the mechanics of Scrum, it’s inherently Lean, a philosophy of work and business that became popular in manufacturing when Toyota was faced with increasing competition and lower profit margins. Now famous, the Toyota Way is a comprehensive system and business philosophy consisting of Lean practices, together with a number of other tools and methods that resulted in the awe-inspiring success that followed Toyota for nearly a century.
Kai-zen
One of the tools, and probably one of the most important ones, that made Toyota turn around their sinking ship into the preferred automobile provider worldwide, is Kaizen, a Japanese word that can roughly be interpreted as building a culture of continuous improvement, like a hoola-hoop that keeps turning around as long as there’s motion.
The word “continuous improvement” however dilutes the meaning in so many ways to me, coming from highly regulated environments where ISO standards were followed and continuous improvement synonymous with unreasonable managers who weren’t involved in the operational side but kept raising the bar under the flag of continuous improvement. When I hear the word, it brings up a feeling of resistance in my stomach reminding me how people were expected to do more with less resources, always emphasizing how what has been done was never good enough.
It took me walking away from the corporate world to gain perspective and realize the true meaning of what continuous improvement is really about and why it made Toyota so successful.
If Kaizen, or continuous improvement, is not working for you, it’s possible that the meaning of the word has been lost or misunderstood. Here’s how to build a culture of Kaizen and improve agility.
A Habit Of Improvement
Kaizen is a habit. Kaizen is a culture. Kaizen is a tool to make life easier. It’s a tool to reduce waste.
If it’s not easy, it’s not Kaizen.
Kaizen is usually born out of frustration or bottlenecks in the process. It can of course be applied at any point in the value chain, yet it becomes necessary when there is a build-up at any point in the process.
Kaizen should be applied whenever someone in the team is frustrated. Whether you’re waiting for another team to complete a part of the system before you can continue, or you’re tired of repeating the same, old, boring work over and over again, if it doesn’t feel good, it might be a good cue to look at Kaizen.
So how do you do it right? How do you build a culture of Kaizen?
1. Observe Objectively
There is a saying in the world of quality management that what gets measured, gets done. You’re not able to improve anything if you don’t know how it is currently performing. The first step is to objectively observe the entire process and obtain baseline measures against which improvements are based on.
In manufacturing it is easy to measure time spent on a task or process as everything can be seen. In software development or knowledge work, it’s less tangible and it is up to the team to be disciplined enough to measure their work effort themselves. In manufacturing, the facts speak for themselves. In knowledge work, only you will know whether you were spending that time surfing the internet or really doing the work that you said you did.
The first step is to visualize the work on a Kanban board, as a standard Scrum board is not sufficient to identify process waste.
The second step would be to measure each activity’s duration. As there are always outliers in any process, there should be enough comparable instances to define a reasonable and realistic baseline average before deciding what the improved target should be.
2. Total Flow
The single biggest flaw of industrialization, and also it’s biggest strength, is the fragmentation of work and parts of a system into small, repeatable parts. In a typical company, there is an invisible barrier between Finance and Marketing, between Development and Support, even between requirements gathering and programming.
Each part of the value chain is responsible for one, unique part of the system, allowing them to drill down into detail and optimize on a micro level. Of course, this makes sense and is one of the reasons why it is possible to improve the whole system.
Yet, this is also most often the breakdown of the system, where teams are so focused on their own results and responsibilities that they forget the systemic nature of the organization they are part of.
You’re doing Kaizen wrong if you don’t include the entire value chain in your improvement efforts.
You are as weak as your weakest link and with an average of 10–15% productivity in most software development companies, the cross-team or cross-divisional handovers and relationships are the biggest area for improvement.
Keep the impact on the entire system in mind when improving one part. When an improvement in one area doesn’t result in an improvement in the total lead time, there has been no improvement.
3. Remain Open To Alternatives
Our education system has moulded people who are trying to find the ‘right’ answer, refraining from offering an answer that might potentially be wrong. We’re scared to make mistakes and as a result we’re not open to alternatives offered which doesn’t seem obvious that it might result in an improvement.
Kaizen however requires an openness, a “Yes and” attitude to problem solving, not a “No but” one. When someone offers an improvement suggestion which might not sound like a good alternative, remain open and try it anyway. Refrain from saying no to any solution offered by anyone, whether they are part of the team involved or not. It’s often easier to spot an obvious error from the outside than when you’re part of the team.
View it is a learning experience and allow people to make mistakes. Even if an improvement suggestion doesn’t work, try it and see what you can learn from the experiment rather than seeing it as a failure. Maybe the suggestion didn’t work but it pointed out another improvement area.
4. Do It Now
If you’re waiting for a new resource to join or software to be approved in the new budget year or training, it’s not Kaizen.
Start where you are and work with what you’ve got.
Kaizen is about small changes, things that can easily be done right now as an experiment to see whether it works before investing in resources to build it. In software development it often happens that solutions are identified as things external to the existing environment and a lot of time and money is invested in for example recruiting new people or buying new tools, all which doesn’t make much sense if you’re not even sure whether it will solve the problem yet.
View improvements as experiments. Try a number of small things that can be done immediately. When you walk out of the retrospective, have one actionable improvement suggestion that can be done right away rather than a list of ten that you only talked about.
5. Iterative Process
Kaizen is an iterative process, not a once-off project. Try one thing at a time, measure to see whether it improved the lead time or not, and then try something else. Once you’ve got the results, repeat. Repeat again. And again. And again…
Don’t make too many changes at once as it is hard to see the impact of the change when there are many changes done at one time.
Don’t stop when you’ve reached your target. Targets are meant to be exceeded, not met.
Kaizen is a culture, it’s a habit of continuous improvement. It’s not a destination. Essentially, Kaizen is about building better habits, and the best way to build habits are to make it easy, achievable and repeating it.
Conclusion
For Kaizen to be successful, it has to become a culture. It’s a continuous focus on getting a little better at what you are doing already, everyday. It’s not a constant criticism of what is going wrong and should be changed.
Kaizen is a step-by-step approach to optimizing the total system where small changes are made continuously, rather than big changes done once a year.
How can you improve your work process for the better? Now?
Originally published on Medium: https://medium.com/teal-times/a-culture-of-kaizen-2cb8d4ebd6ba